Again and again I am asked whether it is not possible with the tuning kits we offer for the Yamaha and Bosch e-bikes to raise the power of the motor or adjust the support characteristics according to their own wishes. To give you a sense of what is possible here and what is not, I will therefore explain here the basic operating principle of tuning modules for Yamaha and Bosch drive systems.
Speed Sensor
The current Bosch and Yamaha drive systems are so-called mid-motors. The drive is located here directly at the bottom bracket of the bike, i.e. approximately in the middle of the bike. The limitation of the speed is implemented here via a separate sensor on the rear wheel. This sensor is the key to all available tuning modules for these motors. By the way, hub motors do not have this sensor, since the motor directly actuates the rear or front wheel without further transmission and thus the ridden speed can be measured directly by the motor itself. Hub motors are therefore also often much more difficult or impossible to tune.
By the way, the sensor is a relatively primitive electromechanical component. It contains only a reed contact, a switch that is actuated by a magnet. This sits on a spoke of the rear wheel and briefly actuates the contact once with each wheel rotation. The functionality is identical to a sensor of a normal bike computer.
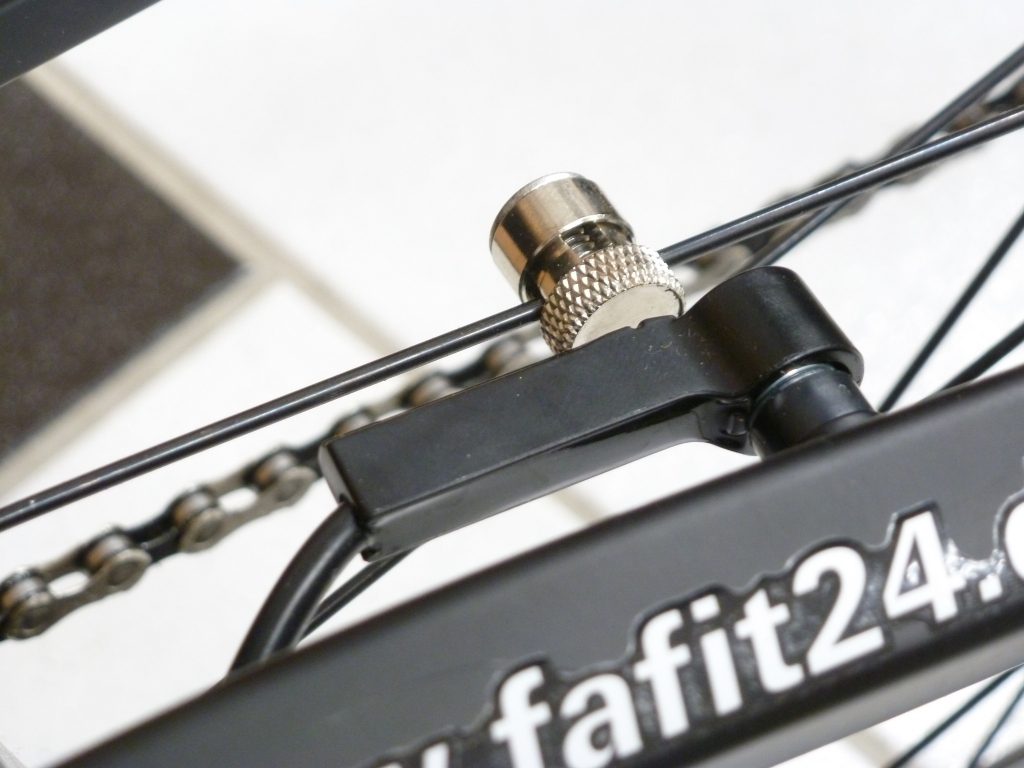
Due to the legal requirements, this sensor is used by the motor control unit to limit and finally completely deactivate the motor assistance on pedelecs from around 25km/h, and on S-pedelecs from 45km/h. The sensor is also used by the motor control unit to limit and finally completely deactivate the motor assistance on S-pedelecs.
Since this sensor is the gateway for many tuning measures, drive system manufacturers are making efforts to prevent manipulation of this signal.
Bosch tamper detection
Bosch has introduced a so-called tamper detection in 2019, which is also installed in older bikes via a software update in the workshop. The sensor signal is checked for plausibility by the motor controller. Sensor values available in the motor are used to check the plausibility of the speed. For example, the acceleration of the bike can be calculated from the signal from the speed sensor and this value can be compared with the measured values of the acceleration sensors installed in the motor. Significant deviations then indicate manipulation. However, a manipulation does not immediately lead to an error, but is tolerated by the motor for some time. In our experience, simple tuning methods, such as the pedal trick described below, cause the error code 504 to appear after about 200 to 1000km. The error causes the motor power to be significantly throttled for 90 minutes of riding. The motor then hardly assists any more. In addition, an error entry is stored in the motor. This means that the error can also be identified later during a visit to the workshop. To prevent the error, it is therefore important that the speed signal correlates as well as possible with the actual speed.
Software tuning
In principle, it would already be possible to change the speed restriction by adjusting parameters in the motor control unit. On the one hand, a smaller wheel circumference could be stored in the motor control, which would reduce the measured speed and thus actually allow the bike to be ridden at a higher speed. It would also be obvious to simply set the limit of 25 or 45km/h to a higher value. With all current Bosch drive systems (Active Line, Active Line Plus, Performance Line CX), the option to change the wheel circumference is available. If you have such a motor you can easily change the wheel circumference on the Kiox, Intuvia or Nyon display by +/-5% yourself. With the Purion display this can unfortunately only the workshop with Bosch diagnostic software. However, you will find that the modification has no effect on the motor support. Only the display values for the distance traveled and speed will change. For example, if you set a 5% smaller wheel circumference, you will only see 23.8 km/h on the display instead of 25 km/h. If the motor previously stopped at 25km/h, you will notice that it now stops at 23.8km/h. The adjustable wheel circumference is used in the Bosch systems only to adjust the display values. The actual motor support limit does not change. With the Yamaha drive systems (PW, PW-X, PW-SE) there is no possibility for the end customer to adjust the wheel circumference. Of course, the wheel circumference responsible for the speed limitation must be stored somewhere in the motor control. At least until now, it is not known how and whether these values can be changed at all in the Bosch and Yamaha drive systems. Even dealers can not change these values. But this does not mean that such a change of the parameters is not possible at all. For many other drive systems, such as BionX, Heinzmann, Shimano E8000, but also the older Bosch Classic, there is very well such a possibility. Mostly, a special device is used for this, which must be connected only once to the bike and then allows the change of individual parameters.
Hardware tuning
All available tunings for these drives therefore realize the removal or offset of the speed limit via an adjustment of the speed sensor signal. Since this always requires additional electronics, I refer to this as hardware tuning.
Pedal trick
You may have heard of simply mounting the speed sensor on the pedal, which is often referred to as pedal trick. One makes use of the fact that at higher speeds the ratio of crank to rear wheel is always greater than 1. The rear wheel therefore turns faster than the crank. In the highest gear, the transmission ratio is around 3 to 4. If the sensor is mounted at the height of the crank so that it detects the crank revolutions instead of the wheel revolutions, the motor control unit calculates a lower speed from this. There have been positive experiences with this type of tuning. However, problems are also reported. Early software versions from Bosch recognized this pedal trick as a so-called 1:1 error with error code 503. Since the motor control can also measure the pedal speed, it only had to compare the measured value with the measured wheel speed to recognize that something is wrong here. However, this error no longer exists in newer software versions. This is probably because it can also happen that the wheel turns at the same speed as the pedal. And this happens in very small gears. Here, depending on the number of teeth on the chainring and the cassette, it can actually come to a 1:1 ratio. Just when someone has adjusted the ratio to his needs, it often came to this notorious problem and for Bosch probably to many complaints. Even if this error no longer occurs with newer software versions, the pedal trick has other consequences. For example, the motor characteristics change significantly, since riding conditions can no longer be detected correctly. For example, if you stop pedaling for a short time, the motor control is always of the opinion that the wheel is stationary. When you start pedaling, the motor will therefore try to start with the same characteristics as if the wheel were stationary. That is, even if you are already riding. The behavior of the motor becomes somewhat rougher. And of course, the display on the wheel only shows incorrect values in terms of speed and distance.
On the Bosch drives with tamper detection, the pedel trick is detected after some riding time and the infamous error 504 occurs.
Clip-on tuning modules
A very sophisticated method to manipulate the sensor signal are on the speed sensor attachable tuning modules. Here, the magnet on the spoke is shifted slightly so that the original sensor no longer detects the magnet at all. Instead, the magnet is positioned so that it is detected by the tuning module plugged onto the speed sensor. The module then switches the original sensor by an integrated electromagnet. Such tuning modules are available from various manufacturers and for almost all mid-motor drive systems. The modules contain a controller that is powered by an integrated battery. Up to a certain speed, usually in the range 15-20 km/h, the incoming impulses from the magnet on the spoke are simply passed on unchanged to the original sensor. So the wheel behaves at low speeds just as if no tuning module was installed. If then at higher speed the tuning intervenes, from these modules often only every second or only one of three impulses of the wheel sensor is passed on to the motor control. As a result, only half or one third of the speed is shown on the display. Accordingly, the measured distance is too small. Of course, you have to judge for yourself if this bothers you. But of course it is not very nice that these tuning modules can be identified without problems in the mounted state.
Permanently installed tuning modules
Permanently installed tuning modules, on the other hand, are usually invisible from the outside, as they disappear either under the plastic covers of the motor or in the frame tubes. These modules in particular differ significantly in terms of their range of functions and installation. Some modules are even supplied in individual parts as a kit and must first be soldered together. There are also so-called “dongles” where only the wiring and a socket are permanently installed. The actual tuning is then simply plugged in. If you decide for a fixed tuning, it is worth a close comparison of the technical characteristics. We know of many customers who have already bought several modules because they were either not satisfied with the operation or functionality or were overwhelmed with the installation.
There are some simple tuning modules for fixed installation on the market that only change the wheel speed sensor signal and therefore essentially have a similar range of functions to the clip-on modules. Of course, these modules are then invisible after installation. Such modules can usually be recognized just by looking at the product illustration. These modules usually have only two connectors. One of them is connected to the wheel speed sensor during installation and the other is then connected to the corresponding input of the motor control unit. In principle, these modules have the disadvantage that no correct values can be shown in the display.
Differently the modules with correct display values. These then have 4 connectors, because on the one hand, as in the above mentioned designs, the sensor signal is adapted to the motor control, but at the same time the data communication from the motor to the display. These modules then also have routines implemented similar to a bicycle computer and measure speed, distance traveled, maximum speed, etc. themselves. By exchanging certain data packets sent from the motor control unit to the display, it is possible to display these values correctly. All VOLspeed modules modify the data to the display, so that correct values are shown as far as possible. In some cases, however, it is not possible to adjust the values because they are calculated by the display itself.
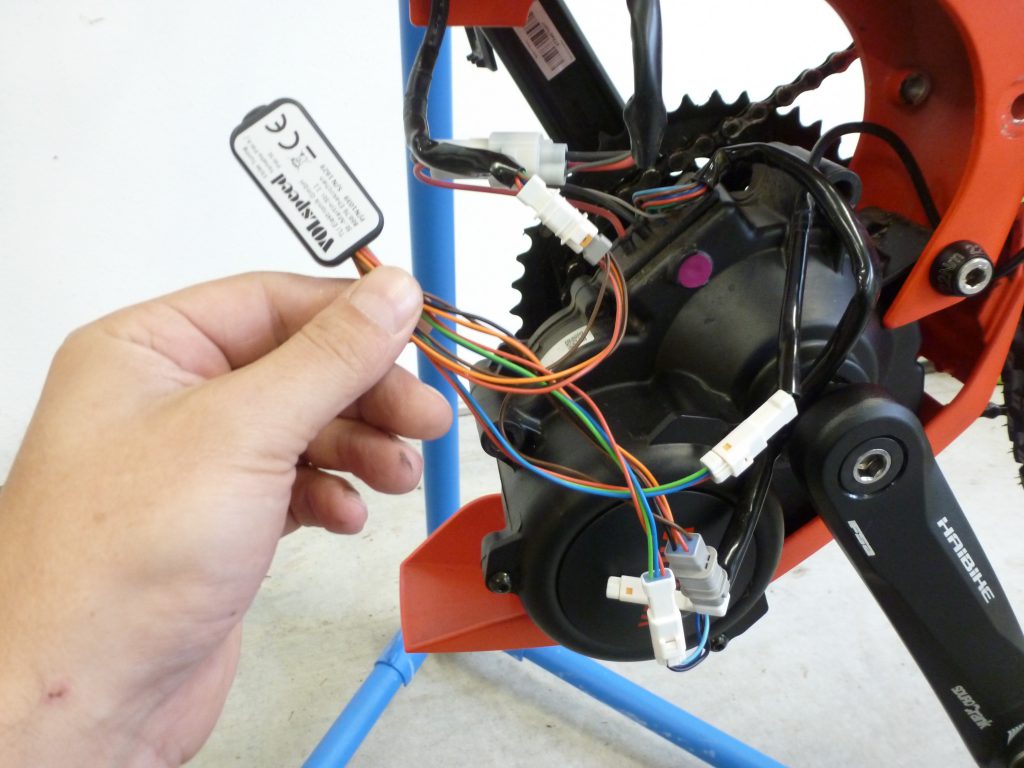
However, the data traffic between the motor control unit and the display contains information that is used by the tuning module. Thus, for example, the keystrokes on the control unit can be evaluated. This makes it possible for settings of the tuning box to be made via these keys and the associated setting values to be shown on the display at the same time. Switching the tuning module on and off is also realized in this way. With all VOLspeed modules, the speed limit can be set via the control unit on the handlebar and the module can be switched on and off. With the Yamaha/Giant tuning modules additionally the wheel circumference can be adjusted. This is also a significant difference to other modules which either do not allow any settings at all or which use a USB or Bluetooth connection to the tuning module for this and therefore a smartphone or notebook and an app is required for the settings.
The km/h-accurate setting of the speed limit in the VOLspeed modules ensures that you can raise the limit only slightly, for example to 32km/h. Due to the still existing, only offset cutoff, you can still precisely dose your own power at the speed limit and drive more sporty, i.e. with more power without having to constantly change the support levels. You will be rewarded with a higher range. Since the adjustment is done via the control unit on the bike, you can also adjust the limit easily on the road, since you do not need a smartphone or notebook.
From my own experience and also from many forum posts, I know how annoying the sudden cut-off of the drive motor at 25km/h is for many. This behavior is also called the “wall effect”, because it feels as if you suddenly hit a wall. Many would like the e-bike to continue to provide support at low power above 25km/h in order to maintain a riding experience similar to that of a normal bike. In addition to the interruption of the motor support, the noticeable pedaling resistance of some drive units is also found to be annoying. All VOLspeed modules therefore have a switchable dynamic mode that significantly reduces this effect. This is particularly noticeable in the higher support levels. The effect is particularly pronounced there, since at the speed limit the previously high support suddenly breaks away. To understand how this works, you need to know that the support does not actually stop so suddenly at a certain speed, but that a limitation takes place over a band of 2-3km/h. This is why it is important to understand that the support does not stop so suddenly at a certain speed. For example, if the support of a bike stops completely at 27km/h, the power is limited from 24-25km/h. However, this narrow band of 2-3km/h is not limited by the speed of the bike. However, this narrow band of 2-3km/h is still perceived as very disturbing. If you increase this band to twice the range, the support at the limit is creeped out much more smoothly and the wall effect is reduced. This is exactly what is achieved by the dynamic mode of the VOLspeed modules. This mode can be activated independently of the set control speed. It is therefore also possible that support is only reduced slowly from 32km/h.
Conclusion
The tuning is realized on all newer Bosch bikes with Active-Line, Active-Line-Plus, Performance-Line or Performance-Line CX, but also on Yamaha bikes with PW, PW-SE or PW-X always by adjusting the speed sensor signal. Thus, depending on the tuning module, the riding behavior can also be changed significantly. At the same time, however, it should have become clear that this does not raise the maximum power of the motor. And that’s why it’s no problem to raise the speed limit with a tuning module, but that doesn’t necessarily mean that you’ll also reach this speed. You can easily reach 40km/h with a e-bike. Beyond that, however, the gear ratio must also be adjusted on many bikes so that you can ride higher speeds with an acceptable cadence. But even then you will find that the 250W maximum continuous power of the pedelec motor is another limitation here and despite tuning simply not much more goes.
I hope to be able to give a halfway understandable insight into the functioning of tuning modules here and would of course be pleased about a visit to our store www.volspeed.de .
By the way, our modules are manufactured in Germany. Each module is also tested for functionality before delivery. If something does not work, we are available by phone and email for questions.